Engineering innovations in the plasma fractionation process
Jacketed vessels, minimizing classified areas, and the inclined plane system
Technical file
Type of innovation: Procedure; System
Scope: Bioengineering
Innovation leader: Shared leadership
Year: 1995
Period: 1972-2002
Geographical scope: International
Economic impact: High
Level of innovation: Disruptive
Patent: Yes
Interdisciplinary connections: -
Plasma fractionation involves subjecting plasma solution to variation in its physical and chemical conditions in order to separate the different proteins of which it consists into plasma fractions. To achieve this, the processing tanks must be kept at low temperatures, something that was traditionally accomplished by refrigerating the entire workspace where the tanks were located. Grifols implemented a number of improvements to minimize the extent of the refrigerated zone, reducing both the costs of cooling its facilities and the need for staff to work at very low temperatures.
Jacketed vessels
A jacketed vessel is a container that is surrounded by a system which contains fluid that is used to cool or heat the vessel’s contents. Although this technology was already widely used in the chemical sector and in the food industry (to pasteurize milk or ferment wine, for example), Grifols was one of the first to apply it to plasma fractionation.
The initiative was prompted by the move from the company’s small Barcelona fractionation plant to the far larger and more modern facilities at Parets del Vallès in 1972. As part of the move, Victor Grifols i Lucas led a project to identify potential improvements to Grifols’ industrial processes.
In addition to improved workplace safety and reduced energy costs, the introduction of jacketed vessels facilitated the maintenance process as the non-refrigerated areas could be cleaned with water, something that had previously been impossible at sub-zero temperatures. This innovation was soon copied by other companies in the sector and, in 1982, when Grifols entered into partnership with Alpha Therapeutic Corporation, one of the leaders of the US plasma products sector, Alpha adopted the jacketed vessel system and applied it to its own plasma fractionation process.
Minimizing clean zones
A clean zone is an area that has been specially designed to ensure low levels of contamination. This is achieved through strict control of environmental parameters, including temperature, humidity, light, and pressure, and by using air flow and filtration to eliminate particles. As a result, clean zones are expensive both to install and to operate.
Grifols realized that, by the simple expedient of making the clean zone smaller, it could significantly reduce those costs. The solution involved isolating the access to the interior of the fractionation reactor, thus reducing the size of the area where special treatment of the air was required, enabling the bulk of the reactor to be located outside of the clean zone. At the same time, operatives had easy access to the technical zone to maintain the machinery associated with the reactor.
By making better use of the space available, the solution led to a doubling of fractionation capacity. The new technology was granted a license by the FDA in 1995, and this was soon followed by similar licenses for the production of albumin and other plasma derivatives, and for successive extensions of the Parets del Vallès manufacturing plant.
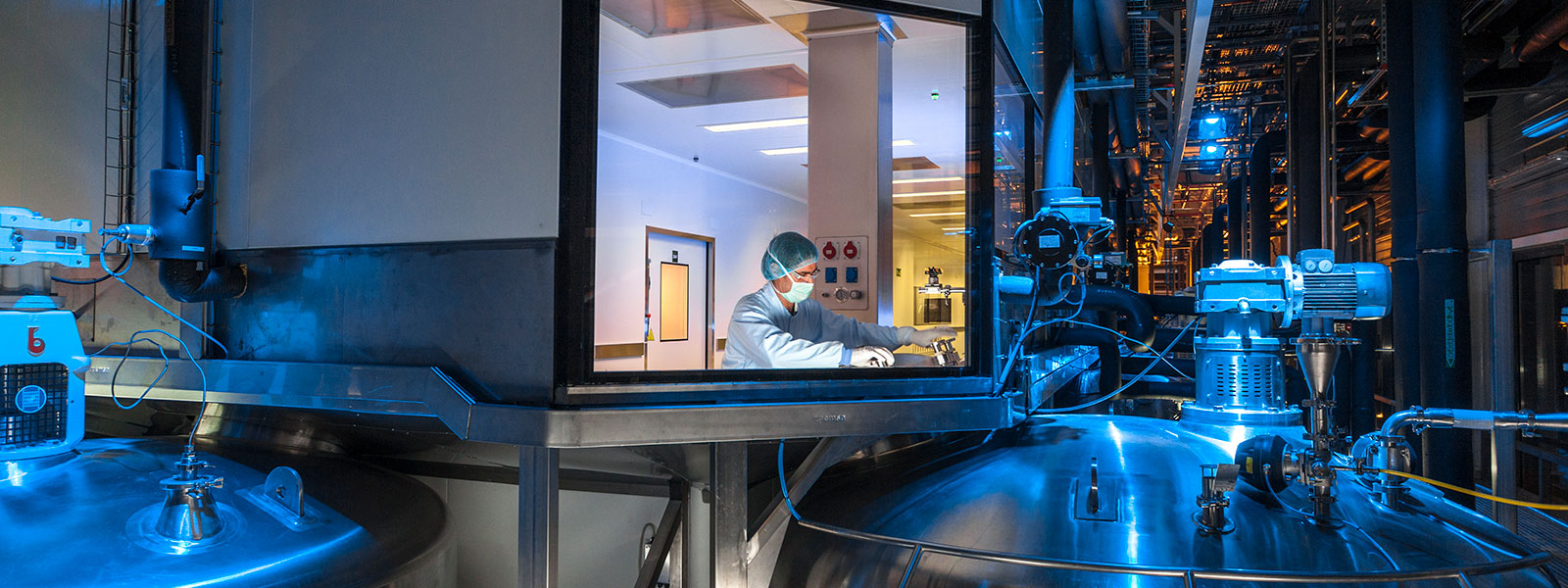
The inclined plane system
Another significant contribution to optimizing the plasma fractionation process was the system of inclined planes, facilitated by an elastic joint at the reactor inlet. The use of this system meant that production areas could be separated into two adjacent zones – a technical zone and a clean zone – while the reactor rested on load cells so that the weight could be monitored throughout the process. The system was patented in 2002 and remains the only one of its kind. It has been sold to third parties both as a basic engineering solution and as a complete offering, encompassing implementation and start-up.
“In addition to improved workplace safety and reduced energy costs, the introduction of jacketed vessels facilitated the maintenance process as the non-refrigerated areas could be cleaned with water, something that had previously been impossible at sub-zero temperatures.”
Bibliography
Roura Adell, S. y Twose Roura, J.I. (2002). Perfeccionamientos en las instalaciones de depósitos de reacción y mezclas de productos para la industria farmacéutica. (Oficina Española de Patentes y Marcas Patente Nº ES20020002803). Link .
Avellà, R., & Miquel, B. (Eds.). (2015). Cuando un sueño se cumple. Crónica ilustrada de 75 años de Grifols. Barcelona: Grupo Grifols, S.A.
Fleta, D. (2019). Grifols concepts for Fractionation. Barcelona: Grifols Engineering, S.A.