ABO® and PBO®
Automated systems to open plasma bags and bottles
Technical file
Type of innovation: System
Scope: Bioengineering
Innovation leader: Shared leadership
Year: 2000
Period: 1972-2002
Geographical scope: International
Economic impact: High
Level of innovation: Disruptive
Patent: Yes
Interdisciplinary connections: -
Plasma products play a vital role in treating a wide range of chronic, rare, or emerging diseases. However, the manufacturing process for these biological medicines is long and complex, and safety is the number one consideration. As late as the 1990s, the first stage of the manufacturing process – opening and emptying the bags and bottles of plasma – was performed manually. Aware of the heightened risk both of product contamination and of injury to workers, Grifols decided to develop an automated solution.
ABO®: the automatic bottle opener system
Manually opening and emptying frozen plasma containers required operatives to work at very low temperatures, and also exposed them to the risk of injury from the sharp implements used to cut open the containers. The first stage, developed by Víctor Grifols i Lucas and the applied engineering team, automated the process of cutting the tops off the plasma bottles. This was followed, in 2000 and 2001, with major innovations that also automated the process of emptying the bottles. The bottles of frozen plasma were fed into a tunnel. Inside the tunnel, the bottles were sprayed with hot water to thaw the layer of plasma in direct contact with the wall of the bottle to facilitate its removal. The bottles were then washed and dried before being cut open. Finally, a robotic arm picked up the bottles and emptied the plasma into tanks.
Perfecting this process was no simple matter. Plasma is a very unstable substance and it was therefore essential to precisely calibrate the temperature and duration of every aspect of the process to ensure that the product could be removed from the opened bottles without deteriorating. This was initially achieved using a manual prototype; however, this prototype did not automate the final stage of emptying the bottles, and a fully automated version was only developed after close multidisciplinary collaboration between the engineering team and the technicians at the production plant.
Internal innovation for external clients
Once the ABO® system had been developed and fine-tuned, it was also marketed to external customers. The first of these was a German pharmaceutical company, who learned about the innovative system and the benefits it offered as a result of a reciprocal auditing process. To date, almost 20 ABO® systems have been purchased by third parties.
From bottles to bags
Automating the process of emptying flexible plastic bags was to prove even more challenging. However, a breakthrough came following a visit to the facilities of Sanquin (Netherlands) and CAP DCF (Belgium) to install ABO® systems. Both companies used roller systems, and this approach provided the basis for automating the process of opening and emptying plasma bags. The result was the Plasma Bag Opener or PBO®, a fully automated system that used a roller system to remove and separate the plasma from the bags, emptied it into processing tanks, and separated out the disposable material for management as biological waste.
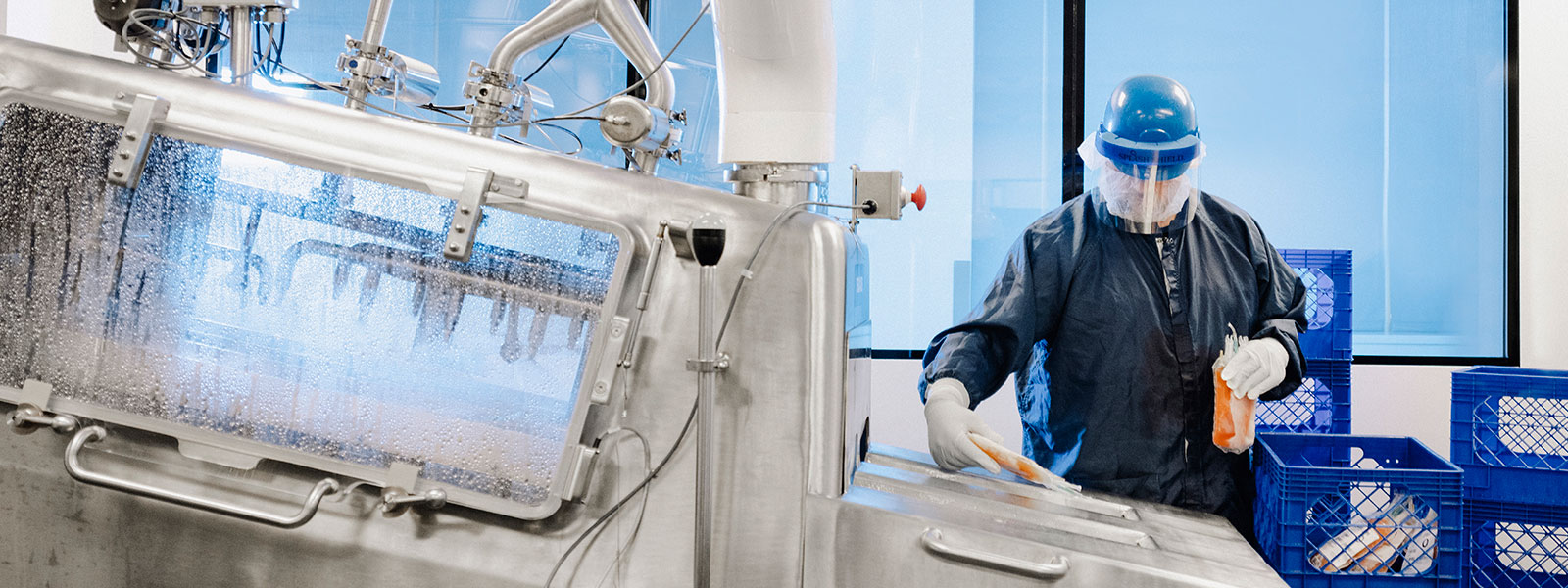
Safety first
The development of the ABO® and PBO® systems was driven by safety considerations. These systems protect the health and safety of operatives, removing the need to work at very low temperatures and reducing the risk of accidents associated with the use of sharp instruments. They also help ensure the safety of the plasma and the products manufactured from it by reducing the risk of bacterial contamination.
“These systems protect the health and safety of operatives, removing the need to work at very low temperatures and reducing the risk of accidents associated with the use of sharp instruments. They also help ensure the safety of the plasma and the products manufactured from it by reducing the risk of bacterial contamination.”
Bibliography
Roura Adell, S., Sánchez Sabaté, J.R. y Grifols Lucas, V. (2006). Procedimiento y aparato para el vaciado de recipientes de plasma sanguíneo. (Oficina Española de Patentes y Marcas Patente Nº ES2245836). Link.
Roura Adell, S., Faba Vilella, M. y Boira Bonhora, J. (2011). Dispositivo para vaciar una bolsa de producto de sangre. (Oficina Española de Patentes y Marcas Patente Nº ES201131265). Link.
Roura Adell, S., Faba Vilella, M. y Boira Bonhora, J. (2011). Método y dispositivo vaciador de bolsas de producto sanguíneo. (Oficina Española de Patentes y Marcas Patente Nº ES2370884). Link.
Grifols, S.A. (2013, april). Plasma Bag Opener, PBO®. Nuevo desarrollo de Grifols Engineering para el lavado, la descongelación y el vaciado de bolsas de productos biotecnológicos. [Press release].
Boira Bonhora, J., Casanova Montpeyo, O. y Pages Becerra, D. (2017). Dispositivo automatizado vaciador de bolsas de producto sanguíneo congelado. (Oficina Española de Patentes y Marcas Patente Nº ES20170382526T). Link.
Oriols Gaja, J., Fleta Coit, D. y Gomez Flores, J.L. (2017). Dispositivo automatizado vaciador de recipientes equipado con medios para la recolección y el vaciado por gravedad de recipientes y que dispone de una zona de recolección de producto. (Oficina Española de Patentes y Marcas Patente Nº ES20170382714). Link.
Oriols Gaja, J., Fleta Coit, D. y Gomez Flores, J.L. (2017). Aparato vaciador por gravedad de botellas que contienen producto sanguíneo congelado con una unidad de comprobación de vaciado y procedimiento de vaciado. (Oficina Española de Patentes y Marcas Patente Nº ES20170382713). Link.